Oslo Opera and Ballet House in Oslo, Norway
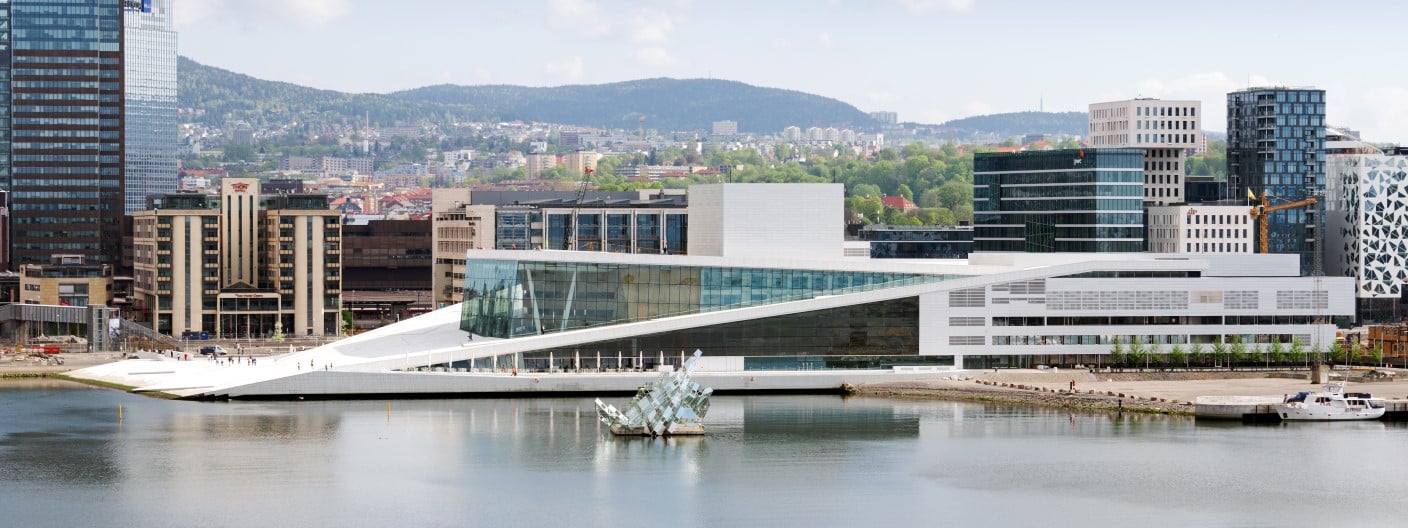
The Oslo Opera House (Operahuset in Norwegian) is home to The Norwegian National Opera and Ballet, and The National Opera Theatre in Norway. The building is located in the Bjørvika neighbourhood in the center of Oslo. It is run by Statsbygg, a governmental building agency that manages properties for the Norwegian government.
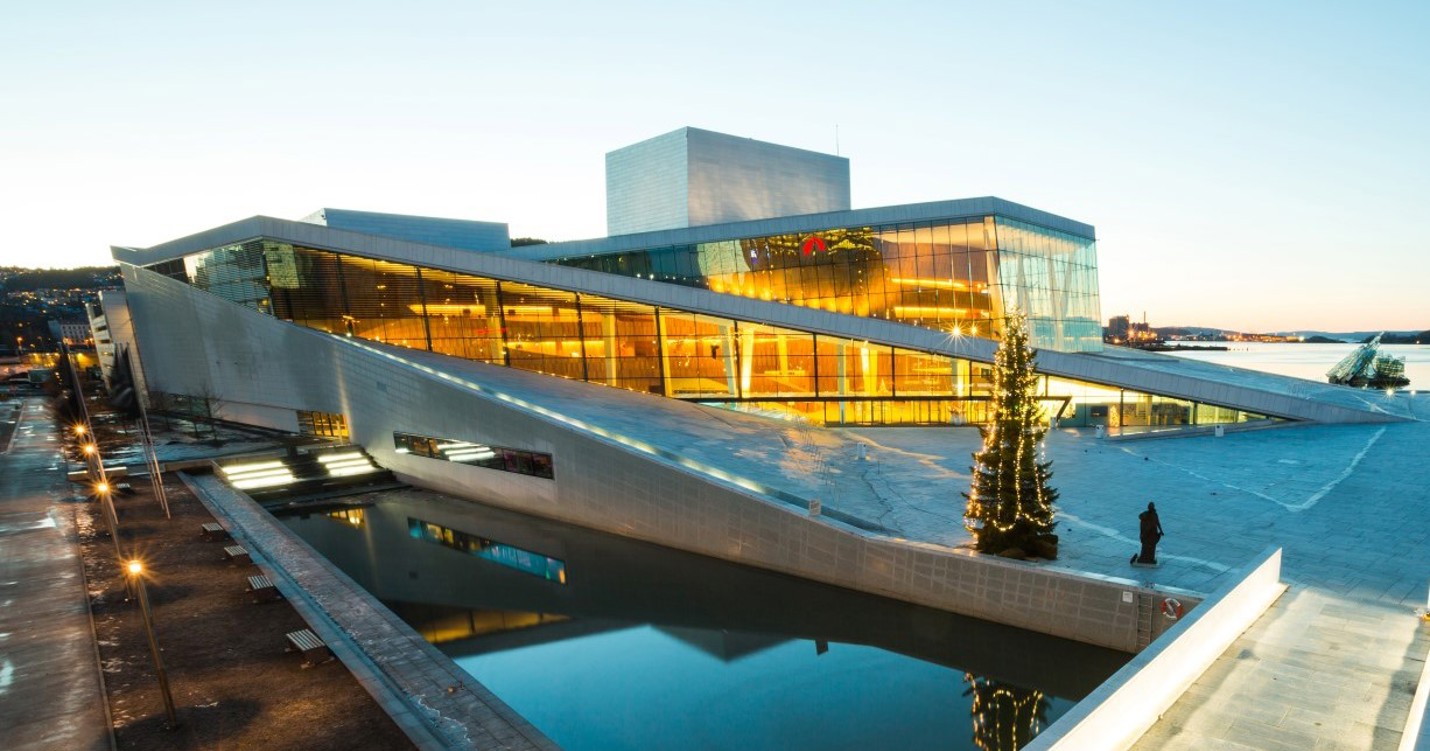
"Its accessible roof and broad, open public lobbies make the building a social monument rather than a sculptural one."
— Snøhetta
Quick facts
Location: Oslo, Norway
Area: 38,500 m2
Completed: 2008
Architects: Snøhetta
Awards: World Architecture Festival Cultural Award in 2008, Mies van der Rohe award in 2009 and several architectural and similar awards
Systems: demand-controlled ventilation (DCV), mixing ventilation and displacement ventilation
Background and challenges
In 1999, a nationwide debate took place and the Norwegian legislature decided to build a new opera house in the city. After receiving 350 entries, the international architects from Snøhetta were commissoned for the project. Craig Edward Dykers and Kjetil Trædal Thorsen were the two founding partners of the company.
The construction started in 2003 and was completed in 2007 with a budget of 4,4 billion Norsk Krona (US$760 million or £430 million).
The Oslo Opera House has been designed and built using the 'whole building design approach' as follows:
- Reduce the demand for heating, cooling, electricity and ventilation.
- Supply the required heating, cooling, electricity and ventilation in the most efficient way and preferably using renewables.
- Always consider the impact on a whole-building level.
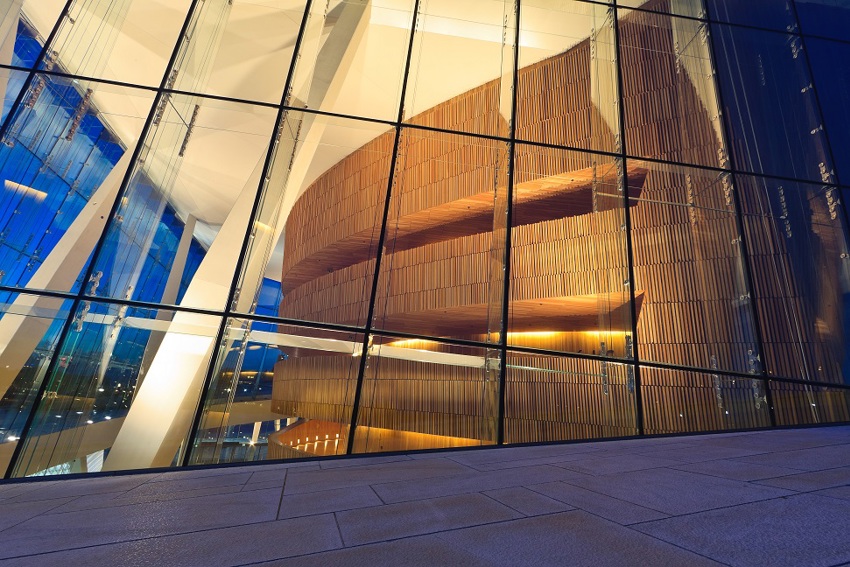
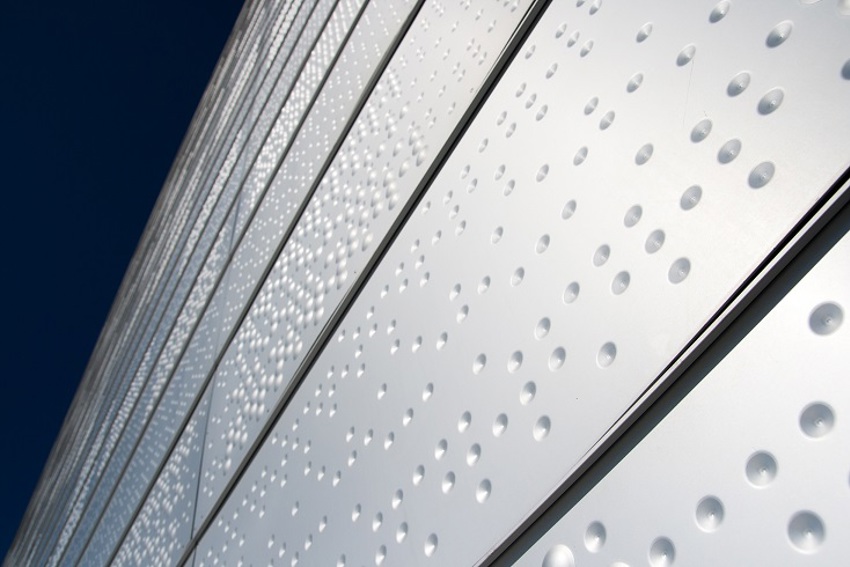
Design of this unique building
The building is 38,500 m² with over 1,100 rooms divided into main sections: audience, rehearsal rooms, administration and workshops. There are three stages: a main stage with approximately 1,400 seats, a scene 2 with a capacity of up to 440 seats, and a rehearsal and a stage 1 with 200 seats.
The base area of the Opera House is the same as the total area covered by four international standard football fields. Workshops can be divided into hard workshops (for making scenery with carpenters, metalworkers, painters and decorators) and soft (for costume production, make up areas, administration and changing rooms). Surprisingly, there is also a spacious green courtyard for relaxation and concentration.
The roof is open to the general public and is a defining feature of the building as it rises from the fjord. The outdoor roof is covered with Italian marble (looking like a carpet), which retains its brilliance and color even when wet, and has excellent properties in terms of stability, density and longevity.
The glass façade gives a magnificent view of the interior wooden walls and creates a stunning image when illuminated at night. However, a high amount of glazing does not interfere with a very comfortable climate indoors even on sunny days (some days it can be over 30°C indoors).
The 'wave wall' in the foyer represents a threshold where the public meets art and is made of oak wood. The oak wood creates a complex organic geometry and works as an excellent acoustic attenuator.
The floor in the foyer is covered with white Italian marble and the walls are designed to look like a glacier structure with green light coloring at the bottom, such as the Icelandic glaciers shining through the pressed crystal structure at the bottom.
Dancing in the water on the main stage
The main stage has the shape of a horseshoe, which is one of the best shapes for opera and ballet, offering a short distance between audience and artists, good sight lines and an excellent acoustic atmosphere with long reverberation time to prevent high frequency vibrations and volume increase.
The main stage is made of oak darkened by ammonia. In the oval reflector high at the ceiling, the magnificient chandelier is suspended illuminating the room with LED lighting, which looks like daylight, and while acting like an acoustic reflector — scattering and diffusing sound.
The main stage features advanced theater technology and a very advanced electro-acoustic system. The main stage itself (16 x 16 m) is a turnable, with two side stages and a background stage.
The stage can be raised/lowered (using 16 lifts), bringing the most amazing ideas to life. In the modern production of Swan Lake, dancers dance in water basins (created by lowering certain parts of a stage and using rubber mats to contain the water) filled with 5,000 litres of warm water with pumps that remove the water after the play.
The stage curtain was designed based on digital images of crumpled aluminium foil that reflects the colours of the auditorium. The orchestra pit is highly flexible and can be adjusted by height and size using three separate lifts.
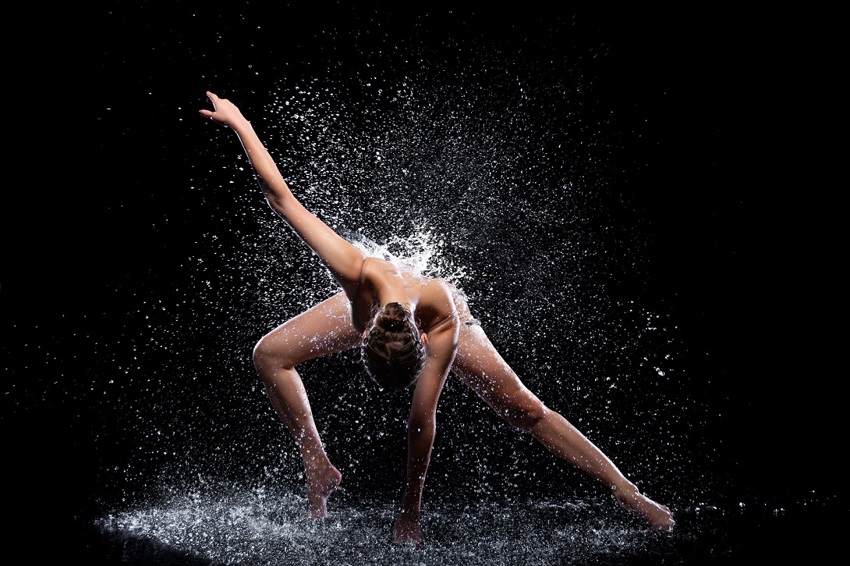
Energy and solar system
The main focus was put on energy-efficient ventilation and energy-efficient light (both with efficient means of control). In addition, the duct systems have very low-pressure drops and thus low energy use. The energy supply is made by district heating, which is the most environmentally-sound solution in a city.
The most visible part of the energy system is the solar cells at the south facades. The cells also provide solar shading of the south facade. Control strategies for glass façade, light, ventilation, heating and cooling are used to improve the use of daylight and passive heating and cooling.
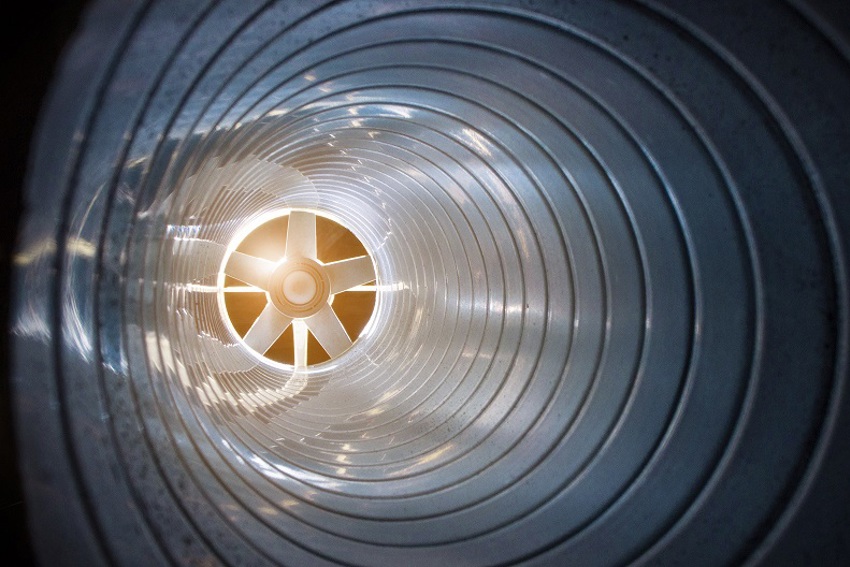
System for good indoor climate
The Opera House has a high maximum ventilation rate due to extreme variation in usage. Further, it is used from early morning to late at night, which causes a long operation time for the units. The users and equipment (such as musical instruments) are highly sensitive to poor indoor climate and require humidity control of the air.
There are 30 ventilation units in the Oslo Opera House, adapted to the use of the different areas. Total airflow is approimately 470,000 m3/h. The different halls have autonomous ventilation systems with variable air volumes. The airflow is controlled by the cooling needs and in addition with CO2 sensors.
The main stage has a maximum supply air volume of 49,000 m3/h and is ventilated with low airflows with pressure chambers under the floor and balconies. The other halls, including scene 2, is ventilated with roof diffusers that have a power distribution pattern. Supply air temperature can be controlled from the desired room temperature or as an outdoor temperature compensation loop.
The ventilation units are equipped with filters, heat and cooling batteries, fans, humidifiers and rotary exchangers.
Workshops and rooms with a high degree of pollution have special features. A number of rooms are additionally equipped with local steam humidifiers that are controlled from each room.
Also the highest requirement in this project was the acoustics with maximum of 17 dBA from ventilation system.
Displacement ventilation
The main theater was designed to hold 1,350 people in audience: 80 people in orchestra and an unknown number of people/equipment on the stage. The decision was to use displacement ventilation under the audience seating and orchestra pit, and mixing ventilation on the stage with controlled temperature between 20-26ºC (supply temperature 20ºC on the first floor and 17ºC on balconies, considering the temperature rise), humidity between 30-45% and CO2 levels below 700 ppm.
The main challenges were supply air units (size and positions in the steps with complex construction), and precise and controlled climate (including high humidity control) in the orchestra pit. Other challenges were in the foyer where there is a large glazed area facing south (570 m2) and the occupancy can be between 700-1,500 people in the evenings when the solar gain is at its peak.
The strategy in summer was to use cleverly hidden displacement ventilation and some extra cooling in balconies, but allowing the temperature rise in the higher places of the foyer. The glazing has solar protection and solar cells. In winter they use floor heating under marble floors, some radiators by floor windows and spoilers at windows and of course the installed windows have a U-value below 1.2 W/(m2.K).
The total energy consumption of Oslo Opera House is above 260 kWh/(m2.a) due to the high load and variable operation. There is also an extensive energy meter system, both for the consumption of electricity and water that allows for detailed follow-up and management of future energy consumption.
Watch: Oslo Opera House — Targets, solutions and challenges
Lecturer: Ida Bryn
Recording from Swegon Air Academy, 2017.
In this video you will find interesting information about the Oslo Opera house and investigation of ventilation system, including:
- Different types of areas in the building.
- Requirements and challenges for design and ventilation system.
- Indoor climate demands such as temperature, humidity, comfort and acoustics.
- Strategies for design and usage of foyer including solar shading, solar protection and ventilation/cooling demands.
Download the full presentation in PDF about this magnificient building (link here).
Learn more from the experts
The building shall stand as a representative institution presenting both Norway's cultural traditions and the Norwegian National Opera's significance in the Nation's culture and society.Parliamentary Bill number 48 (2001-2002)
View more case studies
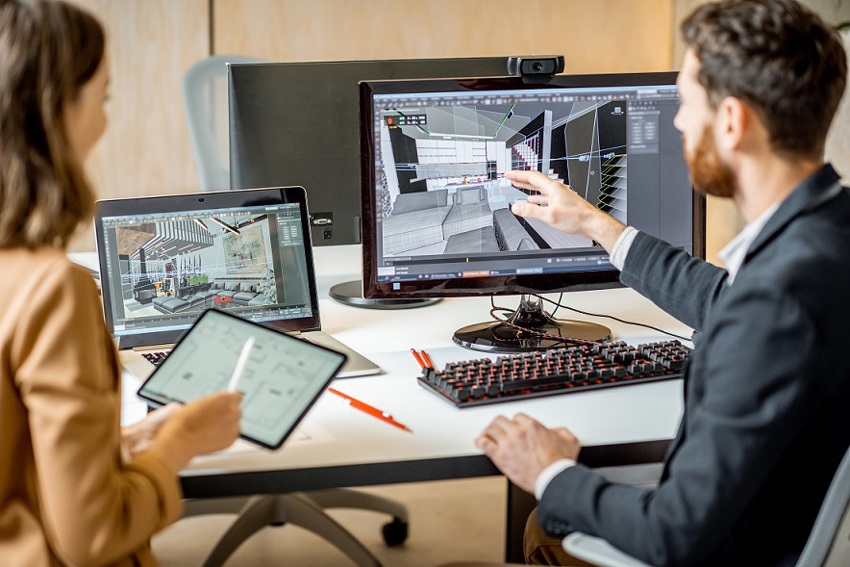
Would you like to know more about building solutions and products?
The supply and extract air diffusers have exceptional sound data, dissemination characteristics and credible documentation. The high induction, low noise level and short throw length of the diffusers meet strict requirements. Thanks to diffusers the opera visitors get goose bumps from the production on stage - not the draft from the ventilation system.
Visit Swegon Group to find out more about detailed solutions, components and products for buildings.
Visit Swegon Group to learn more